長く使い続けられる、確かな品質を生活スタイルに合わせて進化する冷却性能

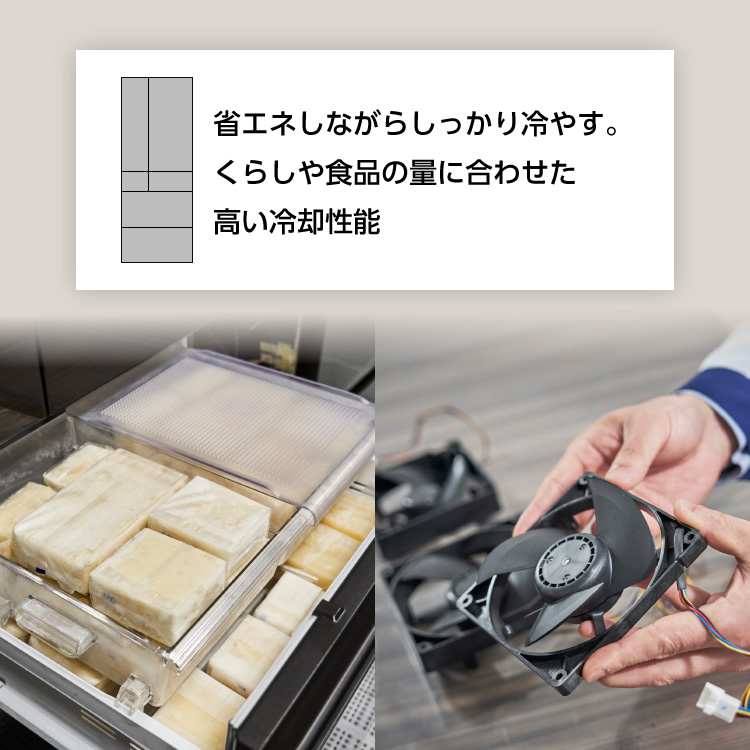
今や「省エネ」はくらしに欠かせないキーワード。24時間365日ずっと働いている冷蔵庫には当然、より高い省エネ性が求められます。「しっかり冷やす」と「かしこく省エネ」を両立するために、どうすればよいか?食生活や保存する食品の量など、時代によって変化するお客様のライフスタイルに合わせ、パナソニック冷蔵庫の冷却性能と省エネ性は進化し続けています。
「しっかり冷やす」の鍵を握るのは「冷却器」「ファン」「ダクト」の3つ
冷蔵庫は、冷気をつくり出す「冷却器」、冷気を庫内に送る「ファン」、冷気の通り道となり庫内に届ける「ダクト」の3つで構成されています。それぞれが省エネ性の鍵を握っていますが、もっとも設計チームが力を入れたのが「冷却器」でした。


庫内を冷やすために「冷媒(れいばい)」という熱の運搬役が、液体から気体へ、また気体から液体へと変化しながら循環を繰り返している。その一連の流れを「冷凍サイクル」といい、その状態変化によって作り出された冷気が各庫内に届けられて冷蔵庫内の冷却が行われている。
庫内を“冷やす”vs霜を“溶かす”。相反する性能を両立させて省エネ性能を上げる
冷却器内には冷媒が通るパイプの周囲に“フィン”と呼ばれる薄い板がたくさんあり、それが冷気を周囲に広げる役割を果たしています。「効率的に冷気を生み出すには、“フィン”の間でいろいろな方向に風がたくさん流れて熱交換が活発に行われるのが理想的。ところがこの“フィン”に霜がついてしまうと風が遮られてしまうため、一時的に温めて霜取りをしなければいけません。冷却すること、温めて溶かすこと。これら相反する二つの働きを、短い時間でいかに切り替えるかが、省エネ性能の重要なポイントなのです」と冷却設計チームの岡本は話します。
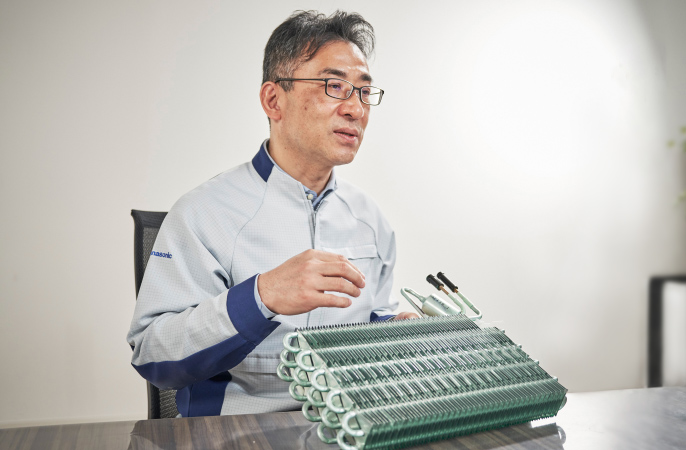
岡本の手元にあるのが「冷却器」。横方向に走るパイプ内に冷媒が流れていて、その周りにあるアルミ製の“フィン”の間に生まれた乱流によって熱交換が起こり、冷気が生み出される仕組み。
霜取りをすばやく行うには、均一に熱を伝えられるようフィンはつながった形状がベスト。しかしフィンがつながっていると風の流れが一定方向にしか生まれず、逆に冷却効率が下がってしまいます。
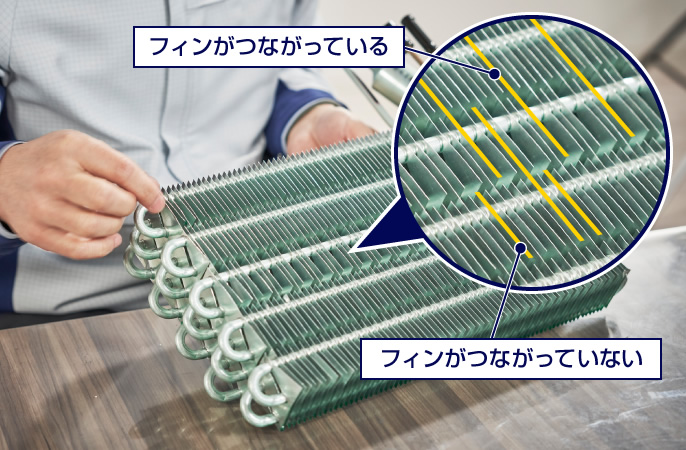
そこで考えたのが、フィンの長さが違うハイブリッド構造です。つながっている部分で霜をすばやく溶かす、つながっていない部分で効率的に冷気を生み出し省エネ性も高める、“いいとこどり”のパナソニック独自の構造は「千鳥配列」と名付けられました。冷却器そのものを自社開発することで、ねらい通りの冷却性能と高い省エネ性能を実現できたのです。
冷蔵と冷凍、異なる温度帯を1つの冷却器でつくられる冷気で緻密にコントロール
冷却器から放出される冷気の温度は約-20℃以下。冷凍室内は約-18℃に設定されている一方で、冷蔵室内は約+3~6℃(「中」設定)であり、冷気と大きな温度差があります。実は、この温度差が冷却器にとっては大きな負担!冷却器から送り出された冷気が冷蔵庫を循環して戻ってくる際、冷気が冷却器にとって“温かすぎる”温度になってしまうため、冷却効率が下がってしまうのです。省エネ性を考えると「できるだけ少ない回数で、冷気を単発的に送る」方法がベスト。そこで、つくり出した冷気を短時間でしっかり庫内に届けるため、「ファン」と「ダクト」の見直しも行われることになったのです。
たくさんの冷気を送り出す「ファン」と効率的に冷気を通す「ダクト」
「『千鳥配列』の冷却器と同時に、ファンとダクトの開発もスタートしました。ファンは内容積拡大の対応を行い、ダクトは空気抵抗を最小限に抑えられるよう内部構造を一新。実は庫内容積アップのために“裏側”のスペースが狭くなることが決まっていて……。大型化したファンが入るのか、ダクトの通風口が狭くなり通風効率が下がるのでは、など苦悩の連続でした。しかし自社で各パーツを開発・製造しているからこそ部門間での“すり合わせ”ができ、実現することができたのです」と岡本は開発当時を振り返ります。
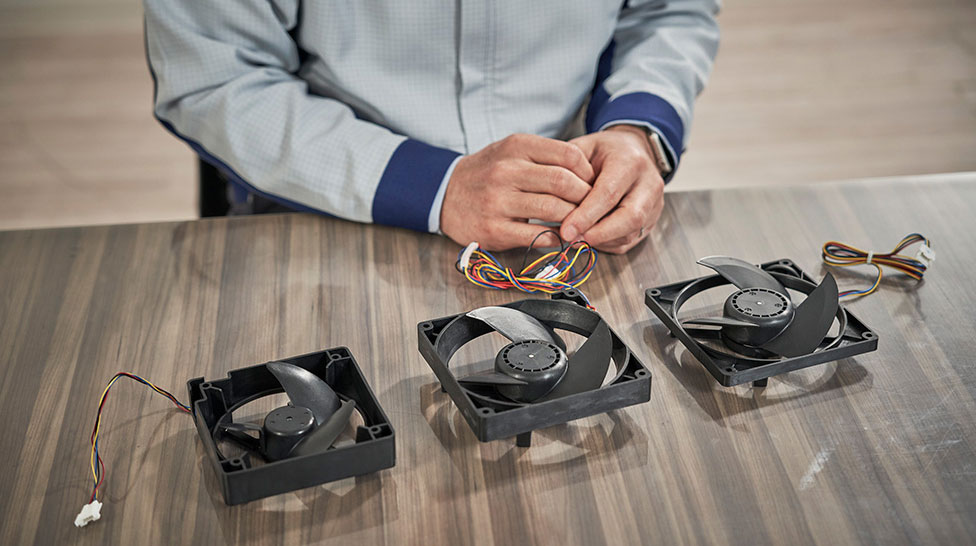
千鳥配列の冷却器と同時に開発されたのが大容量ファン(写真中央)。従来(写真左)のファンに比べ、ひとまわりサイズアップしている。その後、少ない回転数で同等の風量を送り出せる薄型大容量ファン(写真右)へと進化。省エネ性能がさらに高まった。
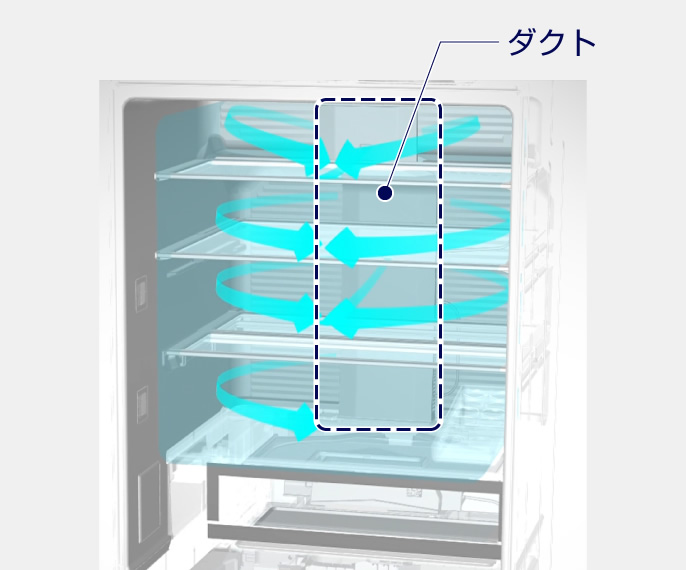
冷蔵庫内を通るダクトには左右に吹き出し穴が。冷却器からの冷気を直接食品に当てると食品が凍ってしまうため、内部の壁に沿って冷気が広がり、庫内全体がやさしく冷やされる設計。吹き出し穴の位置は、庫内を効率的に冷やすためミリ単位で計算されている。
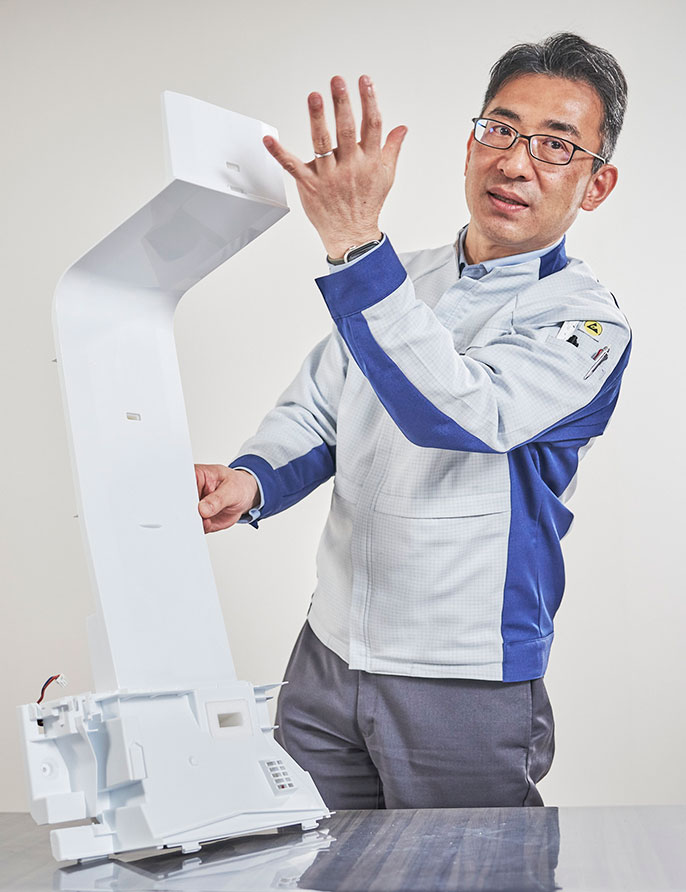
高温多湿な日本の気候に適した冷却性能を徹底検証!
「冷却器」「ファン」「ダクト」…それぞれの性能を高めれば完成、ではありません。「蒸し暑い夏場の頻繁な開閉」「大量に食料品が詰め込まれた状態」など、さまざまなリアルなキッチン環境を再現し、冷却性能と省エネ性を確かめる必要があるのです。そのために行うのが、食品を模した材料を庫内いっぱいに入れて材料内部まで規定の温度まで冷えているかどうか検証する「模擬負荷実験」、室温5℃〜43℃で庫内温度を測定する「恒温室実験」。「特に『恒温室実験』では過酷な環境で行うこともあり、冷蔵庫だけでなく実験をする人間にとってもかなりハード(笑)。ですが、これらの厳しい条件で冷却性能を確かめなければ、お客様に自信を持ってお届けできる製品にはなりません」。
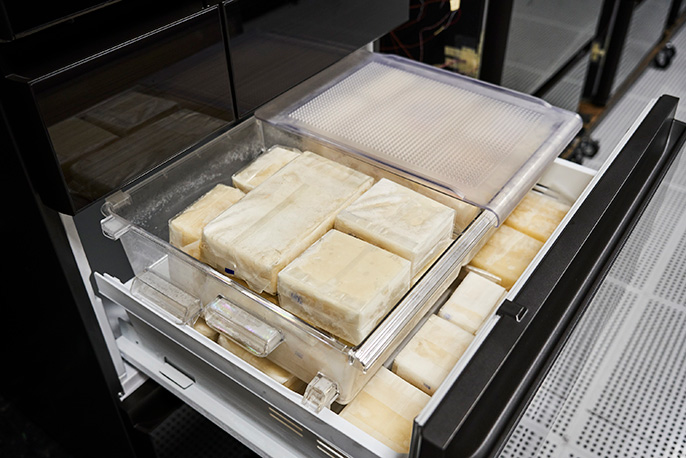
「模擬負荷実験」の様子。食品と同じくらいの水分を含む材料を庫内に入れ、材料が24時間内に規定の温度まで冷えているかどうかを検証する。
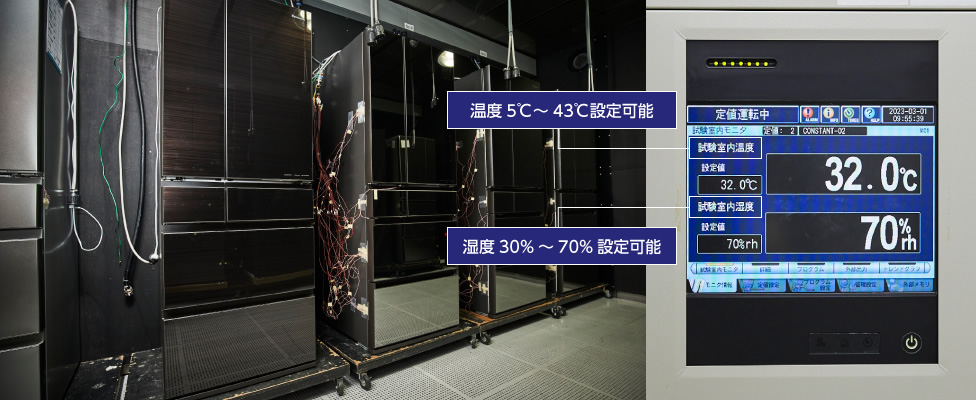
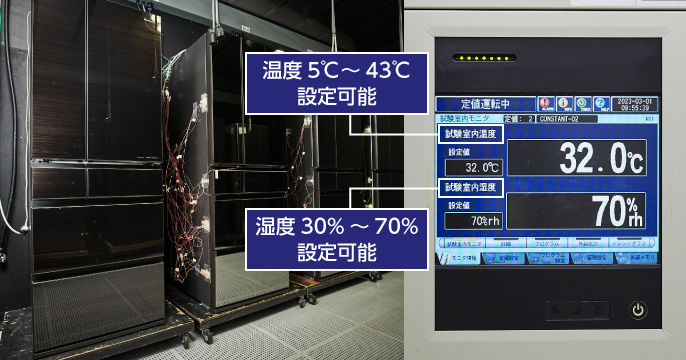
「恒温室実験」の様子。室温と湿度をコントロールできる室内で、庫内が規定の温度に冷えるかどうかをモニタリング。「模擬負荷実験」も「恒温室実験」も新商品で必ず行い、既存商品についても部品変更などがあれば必ず実施。
日本のさまざまな気温、湿度環境でも同じように使っていただけるよう、実験を行っています。