長く使い続けられる、確かな品質を高品質を実現するものづくりの現場
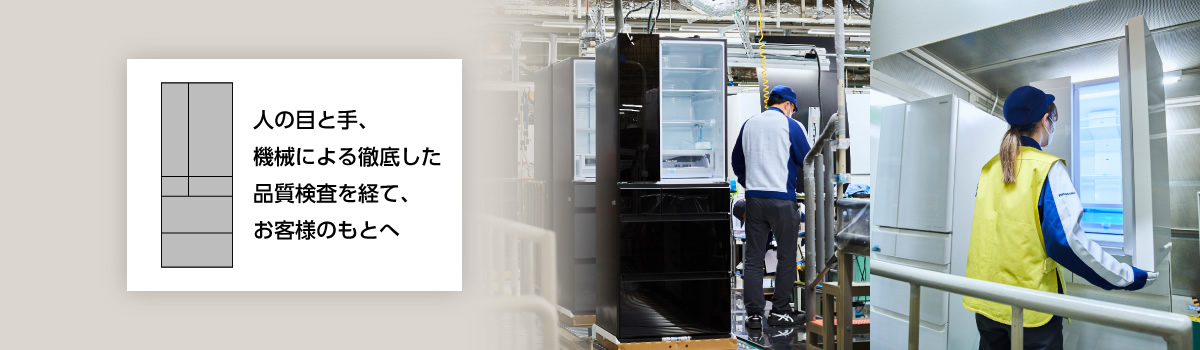
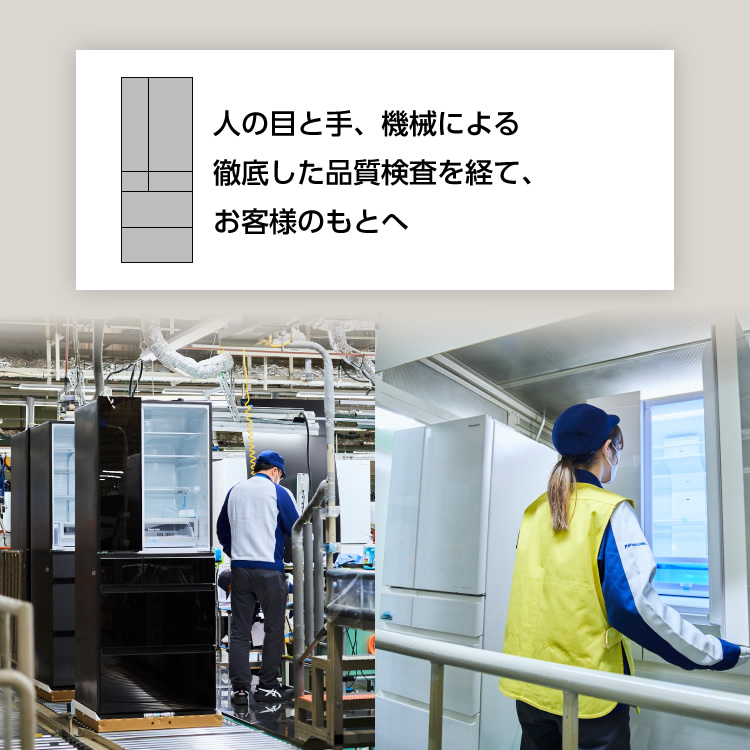
企画・設計はじめとした各部門の奮闘により生み出された製品は、ここでやっと折り返し地点。お客様のもとに届くまで、あとは製造チームに託されることになります。製造チームはパナソニック独自の厳しい品質・安全基準を守る最後の“門番”。いかに正確に・安全に・スピーディに生産するか。「よい製品は、よい製造現場から」を合言葉に、先端技術と人の力を組み合わせ、高品質なものづくりに挑戦し続けています。
「ミックス生産方式」により、さまざまな機種を同一ラインで生産!
サイズ、容量、機能、デザイン…冷蔵庫選びの基準はご家庭によってさまざまです。もし工場で生産される機種の数に偏りがあったら、せっかく選んでいただいても在庫切れになっているケースも予想されます。パナソニック冷蔵庫の生産拠点は、国内では滋賀県・草津工場の一ヶ所だけ。お客様が求められる商品をタイムリーにお届けできるよう、幅広い機種を同一ラインで生産する、独自の「ミックス生産方式」を採用しています。
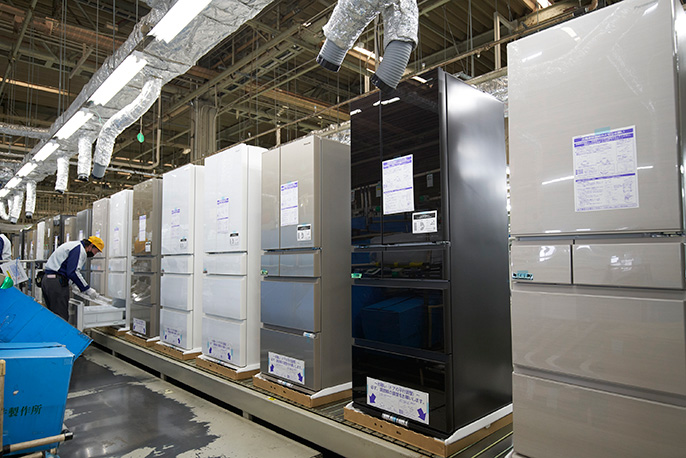
色とりどりの機種が一本のライン上に並ぶ草津工場の生産ライン。国内外に出荷される多様な機種を同時に製造する「ミックス生産方式」により、お客様がどの機種を選ばれてもお待たせすることなくお届けすることができる。
「ミックス生産方式」を支えるバーコード管理技術
「ミックス生産方式」は、実はとても難しい生産方法です。なぜなら同一ラインに複数の機種が流れてくることで各工程で使うパーツや施工内容が機種ごとに異なり、作業が複雑になるからです。万が一、組み込むパーツを間違えてしまうと図面通りの性能・品質には仕上がりません。各工程で作業員が間違いなく作業を行うために、草津工場ではラインを進む冷蔵庫すべてにバーコードを貼付け、1台1台を識別。ライン上に設けたセンサーでバーコードを読み込み、製造する順番をデータで管理。そのデータを各工程とリンクさせて作業員の手元に機種ごとの正しいパーツを届けることで、正確に作業が行われるシステムを構築しています。
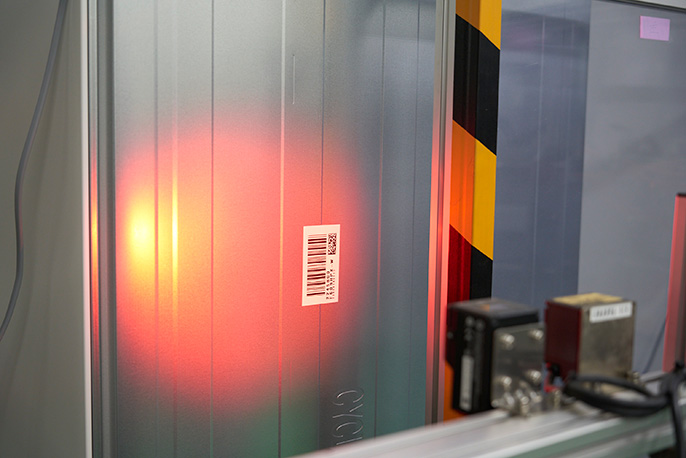
冷蔵庫一つひとつに貼付されたバーコード。生産ライン上ではいわば“名札”のような存在で、さまざまな工程で読み込まれ、パーツ類が作業員の手元に届けられたり、性能検査の結果が記録されたりとデータ管理の要になっている。
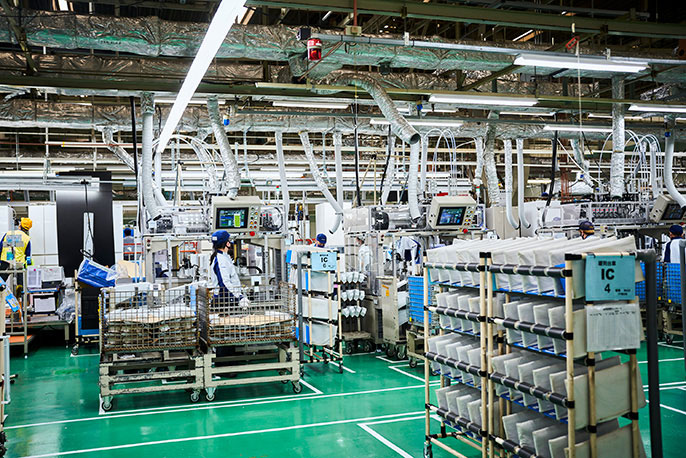
全機種のパーツから必要なものを取り出すのではなく、バーコードのデータをもとに、その機種の担当者がパーツを取り付ける。あらゆる機種のパーツから「探す」「選ぶ」「取り出す」といった手間を省き、効率よく正しく作業ができる。
1台1台確認する「全数検査」を経てお客様のもとへ
「ミックス生産方式」を可能にしているのは、バーコードによるデータ管理だけではありません。工場から出荷する冷蔵庫のうち1台でも不備があってはいけないため「全数検査」を実施。つまり、草津工場でつくられる冷蔵庫は1台の例外もなく、性能・品質検査が行なわれているのです。すべてのパーツが組み込まれた後にライン上で電源を入れ、一定時間で庫内が規定温度まで冷えるか、スイッチが稼働するか、扉が開けっぱなしになった際の警告音が鳴るか、などを機械による測定だけでなく人の目・耳・手でもチェック。冷蔵庫が工場の出口にたどり着くまでには、いくつもの厳しい関門が待ち受けています。
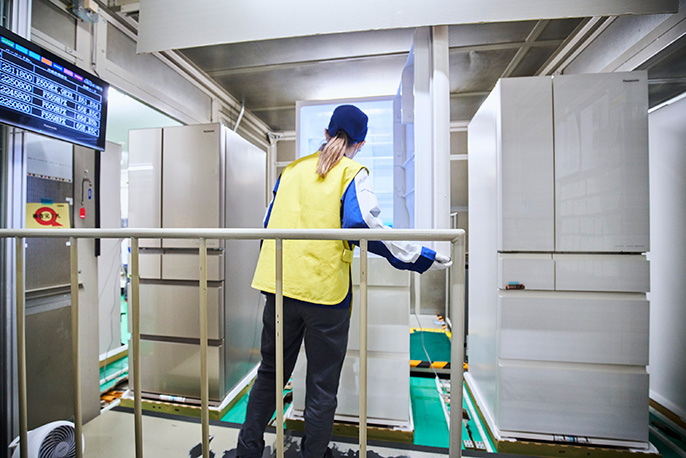
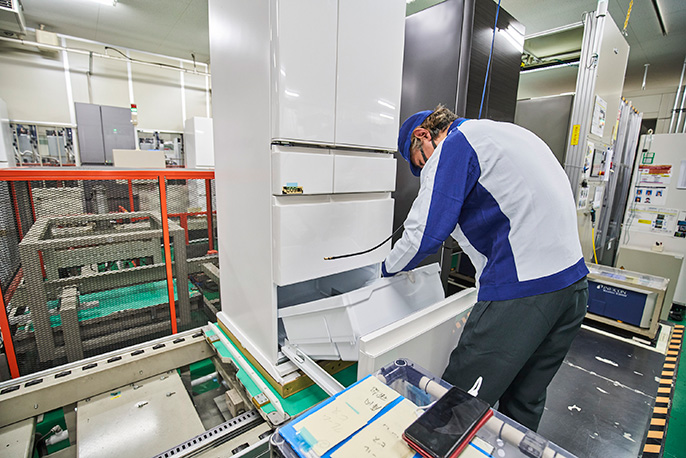
性能検査では、庫内の照明や警告音、スイッチの切り替えなども人の目と耳とでしっかり確認。
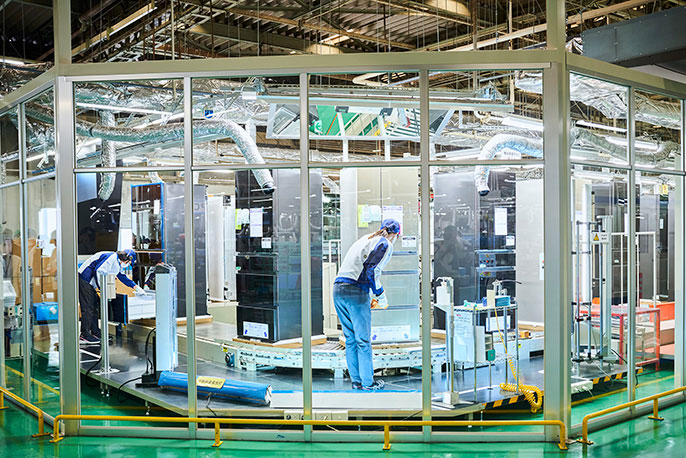
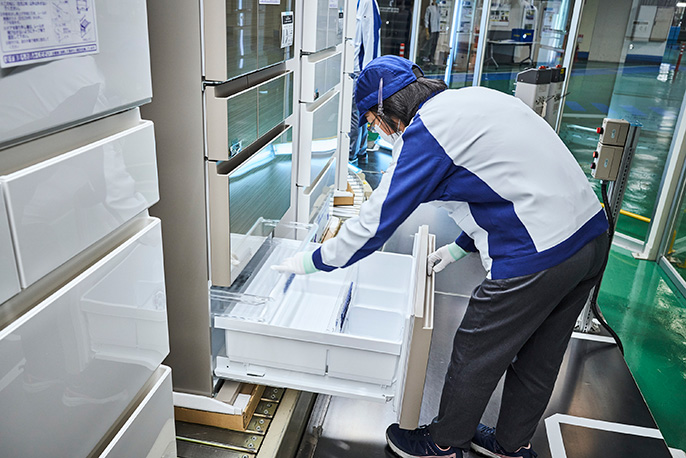
最終工程では画像診断やセンサーなどによる「先端技術の力」と、「人の手」による検査を組み合わせて品質をチェック。先端技術による検査では正確に性能を測定し、さらに人による検査で「引き出しが少し引っかかる」「扉が重く感じる」など数値には表れない微妙な違和感をチェック。「使う人へのやさしさ」を叶えるため、人の感覚も重視している。
食品を入れる商品だからこそ、ものづくりの現場も清潔に
製造現場を進化させることで「ミックス生産方式」を実現した草津工場では、さらなる変革に挑戦しています。「清潔性の高い製造現場」づくり!製造チームの佐々木はこう話します。「冷蔵庫は、食品を入れる家電です。汚れがひどく整理整頓されていない製造現場でつくられた冷蔵庫なんて、お客様も不安ですよね。だからこそ工場を清潔に保つための取組みにはかなり力を入れています。例えば、作業員が着用する手袋を汚れの目立つ白にして頻繁に交換するなど、清潔な環境づくりを徹底しています」
また、工場内での部品の管理についても清潔な管理を心がけています。扉同士が接触して傷がつくことを防止するためにクッションを設置しているのですが、そのクッションを汚れが目立つ白色にして、商品が汚れるリスクを最小限に抑えています。
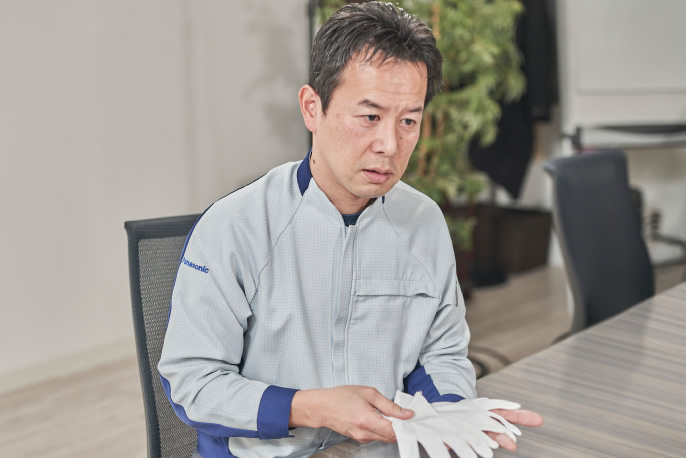
わずかな作業のしづらさも品質低下の原因になる
製造現場の改善のために、働く人の“作業のしやすさ”にも注目。例えば重いパーツを高い位置に設置する工程では、ラインの高さを低くして作業員は台上から楽な姿勢で作業を行えるように見直し。また暗くて閉鎖的だった現場はオープンに周囲を見渡せるようにレイアウトを見直し、明るく心地よい作業環境に。地道な改善活動が日々進められています。「“根性”が美徳の時代はもう古い。品質を一定に保てないというリスクにもつながります。何より大切なのは“誰もが作業しやすい”環境をつくることなんです。作業効率が高まるだけでなく、一つひとつの冷蔵庫への施工品質を高く保つことができます」と佐々木。
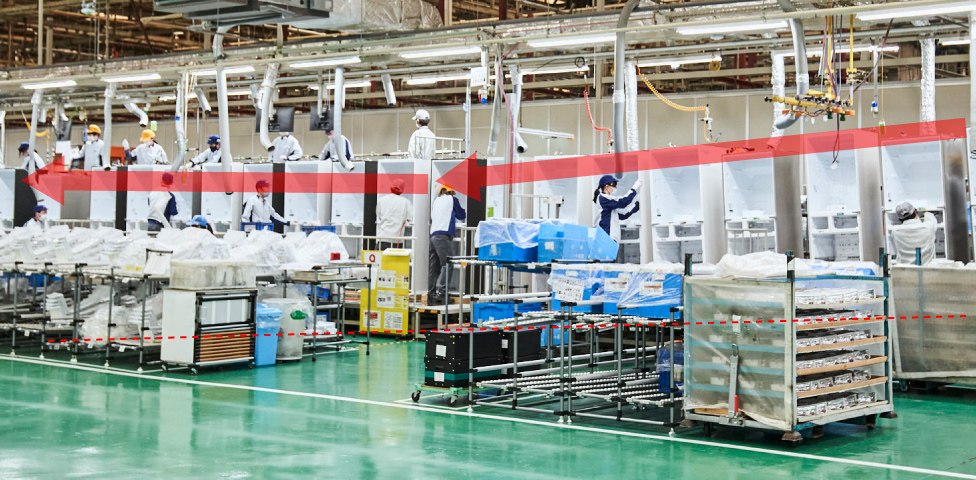
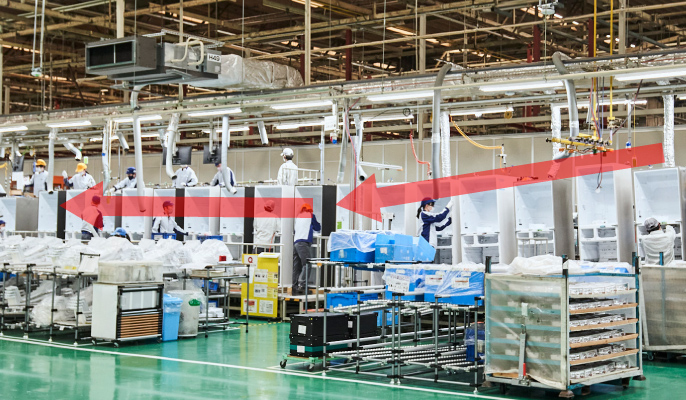
重量のあるコンプレッサーを冷蔵庫上部に設置する工程では、ラインを下り坂にして冷蔵庫が低い位置を流れるようにし、作業員が楽な姿勢で設置を行えるように改善。
切磋琢磨しながらスキルアップにも挑戦!
草津工場の一角にある「モノづくり道場」。実はここ、コンプレッサーを冷蔵庫本体に接続するときに使われる「ろう付」のスキルを磨くための場所なのです。「ろう付」は難易度の高い技能のため、社内資格を持つ作業員だけが任される工程。冷蔵庫だけでなくエアコンなど他の家電でも必要とされることから、パナソニックグループ全体で各家電チームに分かれて互いの技術を競い合う技能大会が開催されるなど、スキルアップを推進する取組みも行っています。
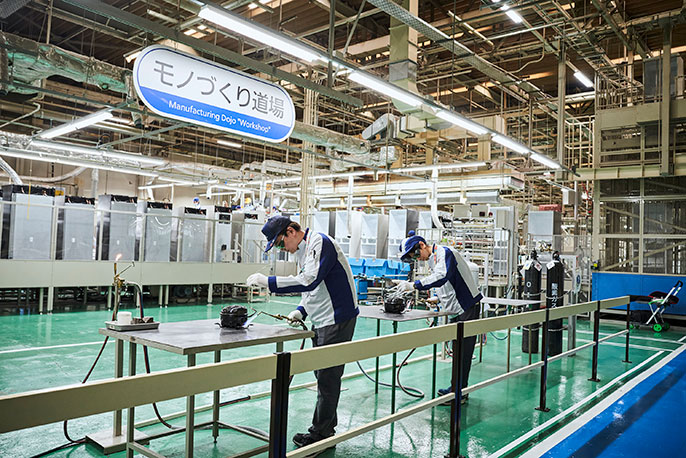
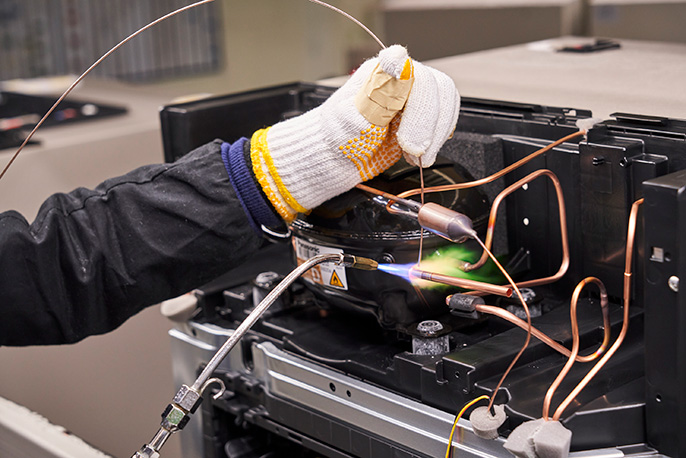
使いやすい収納設計とは?に向き合い新しいアイディアを生み出し続ける機構設計チーム。
省エネと冷却性能の両立に挑戦し続ける冷却設計。
高品質なものづくりと厳しい検査を通してお客様のもとへ冷蔵庫を送り出す製造チーム。
ものづくりのプロセスに関わる一人ひとりの「毎日使うものだからこそ、長年安心して使っていただきたい」という思いを乗せたパナソニックの冷蔵庫は、これからもお客様のくらしによりそい続けます。